- 省力機械の製作・改造 株式会社角田 >>
- 生産工程別省力化提案
各工程の「省力化のチェックポイント」に当てはまる項目があれば、新たな省力機械の導入や、既存の機械の改造、専用治具の開発などで省力化が図れる可能性があります。ぜひ、一度チェックしてみて下さい。
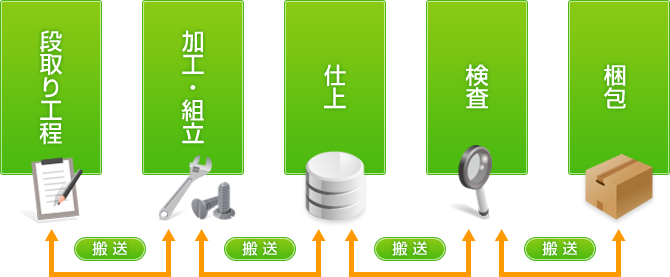
搬送
搬送は次工程に加工物を送る工程ですが、次の作業にスムーズに入れる形で搬送することが重要になります。また、動力も省力化のポイントになります。位置エネルギー(自然落下エネルギー)を活用するのが、最も効率的で省力化につながります。

- 次工程の設備・機械が受け入れやすい姿勢や数量で送られているか?
- 次工程に入る前に、人手で並べ直すなどの作業が発生していないか?
- 搬送時に対象物が転倒、落下することがないか?
- 電気や油圧などで搬送していないか?
段取り工程
生産ラインの入り口にあたるこの部分を改善すると、生産ライン全体の省力化に繋がることがあります。
ここでの時間のロスは、機械の空転時間や作業員の手待ち状態を生む原因になります。

- 材料や部品の整列作業に時間がかかっていないか?
- 材料や部品の整列作業の精度が悪く、不良品がでていないか?
- 重い物や危険なものを、人力でラインに運んでいないか?
加工・組立
ものづくりの中心になる工程です。専用の加工機などを導入している場合、省力化は進んでいると思いますが、それでも見直してみると、省力化の余地はあるものです。

- 外段取りに時間がかかり、機械・設備が停止している時間がないか?
- 治具に加工対象物を固定するのに時間がかかっていないか?
- 加工対象物が動くことによる不良発生はないか?
- 複数の加工・組立工程を一つにまとめる余地はないか?
仕上
加工・組立後の仕上工程です。バリ取りや洗浄、塗装など製品の出来映えを左右する重要な工程です。人間の目が必要になるケースも多く、機械化がしにくい工程でもあります。しかし、ちょっとしたアイデアで省力化が可能になるケースも多くあります。

- 洗浄や乾燥にかける時間が長くなっていないか?
- 多品種化対応に苦慮しており、製品毎に機械・装置を用意して対応しようとしていないか?
- バリ取りなどの作業を人手で行っていないか?
検査
検査と一口に言っても、センサーの下を通過させるような流れ検査、治具に固定して詳細に行う精密検査、人が目視により行う目視検査など、多様な種類があります。特に全数検査を行っている場合は、この工程の処理能力=ラインの生産性になるため、やはり省力化が重要になってきます。

- 流れ検査で対象物の向きが揃っていないため、機器の性能が発揮されていないことはないか?
- 精密検査時の位置決めに時間がかかっていないか?
- 目視検査で対象物を回転させる工程はないか?
梱包
特に多品種小ロットでの生産を行っている場合、製品毎に異なる梱包が必要になることが多く、悩みの種になることが多い工程です。機械化している場合も、手作業で行っている場合も、省力化の観点で見直すと、改善点が多く見つかります。

- 梱包作業を全て、あるいは一部、手作業でおこなっていないか?
- 梱包資材のセットに時間と人手がかかっていないか?
- 梱包済みのものの搬送に時間がかかっていないか?
- 梱包する製品が変わる度に段取りが発生し、梱包ラインが止まることが頻繁にないか?
角田は量産品メーカーではなく、お客様のご要望に合わせた省力機械、省力化機器を一品ずつ作っている会社です。お客様ごとに、課題や解決方法は異なります。またかけられるコストによっても最適解は異なってきます。
ぜひ当社にお客様のお悩みを聞かせて下さい。当社で培った技術やノウハウで、アイデアレベルのものでも、具体的な解決策をご提案し、形にしていきます。