- 省力機械の製作・改造 株式会社角田 >>
- 省力化事例
下記は当社が手がけた事例のほんの一部です。
貴社のお悩みにも角田がお役にたてることがあると思います。
図面や仕様が固まっていなくても、当社の技術者がご相談
にのります。
お気軽にお問い合わせ下さい。
生産ラインの省力化
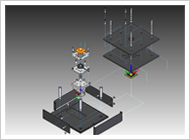

ある電子部品メーカー様の事例です。
検査工程の省力化
検査工程で大きく時間をロスしているというご相談がありました。お話しを聞いてみると、検査をする際に対象物を固定する必要があるが、生産している製品の大きさがまちまちなため、検査する度に対象物の固定に時間がかかっているとのことでした。当社では、検査対象物の大きさが異なっても使用できる固定治具を開発し、検査工程の省力化を実現することができました。

ある電子部品メーカー様の事例です。
洗浄装置の改造
製品を加工した後に、製品を乾燥させる工程がありますが、この乾燥工程の時間を短縮し、乾燥ムラを無くしたいというご相談でした。この部品は、端子が何百個もあるもので、熱風が当たりにくい箇所がどうしても出てしまい、乾燥時間を長く設定せざるを得ませんでした。
お客様で実験をした結果、ある角度で熱風を当てれば、短時間で乾燥させることができることが分かっていましたが、コストをかけずに製造ラインから乾燥工程に最適な角度で製品を搬入させることができずに困っていました。
当社の技術陣が検討した結果、現在の乾燥工程で使用している機械を改造し、固定・振動する治具を作成すれば問題は解決することが分かりました。
機械改造、治具の作成を行い、お客様は最小の投資で乾燥工程の時間の短縮、乾燥ムラによる不良発生の低減を実現することができました。
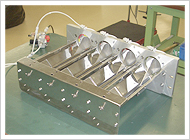

ある食品メーカーの事例です。
容器の蓋を溶着する機械
今度発売する新製品は、既存の製品の容量を少なくしたものを考えていました。しかし、容器に食品を入れ、蓋を溶着する機械はこれまでのサイズに最適化したもので、そのままでは使えませんでした。新たな機械の導入も検討されましたが、コスト面で合わないという結論になりました。新製品の発売の時期が迫っているなか角田に相談が寄せられ、当社の技術陣が検討した結果、既存の機械の改造で対応できることが判明しました。
同時に食品を容器に入れる工程から、蓋の溶着工程までを見直し、最適な治具を導入することでさらに生産性が上がることがわかり、その提案をいたしました。
納期にも間に合い、省力化を実現することができました。
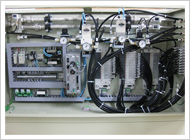

自動車組立ラインの事例です。
空気圧回路の制御装置の改造
自動で塗装する装置を使用していましたが、車種の変更に伴い、この装置で塗装しなければならない色が変更になりました。塗料は空気圧を用いて制御しています。複数の塗料を合成したり、吹き付けるタイミングを制御しないとうまく塗装することはできません。
これまでの装置をそのまま用いると、塗装がうまくできないことが判明し、当社に改造の依頼がきました。完成に至るまで、仕様が二転三転しましたが、その度にお客様と綿密な打ち合わせを行い、生産開始に間に合わせることができました。
お客様は大きなコスト負担無しに、新製品への対応をすることができました。
手作業の自動化
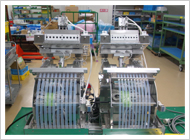

ある電機メーカー様の事例です。
部品供給装置の改造
生産工程で、組み付ける部品を人が一個ずつベルトコンベアに置いている工程がありました。人件費がかかるのはもとより、置いた部品が途中で倒れたりすると、その度にラインが停止してしまうことがありました。当社に、この工程を機械化できないかという相談が寄せられました。
当社で、上部に部品をストックしておいて、ラインと連動しながら一個ずつ、倒れない状態で部品を供給する装置を提案いたしました。
その結果、4人で作業していたラインを2人にすることができ、また部品の供給ミスによるラインの停止もほぼ無くなりました。
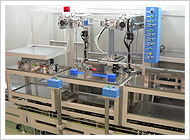

ある金属部品メーカー様の事例です。
重量物を移動・反転させる機械
組立てラインの中で60kg以上もある部品をラインに載せる工程がありました。作業員が3人がかりで載せていたそうです。また、上側の組立てが終わった後に、下側の組立ても行わなければならないのですが、その際にも3人の作業員が抱え上げて、部品を裏返していたそうです。組立ては1人で行えるものの、部品を動かす際には、周囲の作業員の手を止めて応援を呼ばなければならず、効率が悪い状態でした。また、これまでは大きな事故はありませんでしたが、部品の移動中の事故も心配でした。
当社では、重量物をラインに載せることはもちろん、途中で自動的に反転する機能を付加した装置を開発し、納品しました。
これにより、作業途中で手を止めなくても良くなり、作業効率が向上したことはもちろん、職場の安全性を向上させることもできました。
さらに、より大型の製品を作成できるようになったということで、取り扱い製品も増えたそうです。
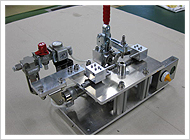

ある電球メーカー様の事例です。
治具による効率化
電球には、「口金」と「はとめ」と言われる部品がありますが、これまでは別々に作業員が手作業で組み立てていました。当社では「口金」と「はとめ」を機械で一度にかしめられる治具を開発しました。全てのラインを自動化することも可能だったのですが、
お客様の予算の都合でそれは難しい状況でした。そこで装置の改造は行わず、治具の作成のみを行い、2工程を1工程にすることにしました。
一番時間がかかっているこの工程を半自動化することにより、最小のコストで生産ラインの効率化を図ることができたと喜んでいただいております。
機械・装置の改良
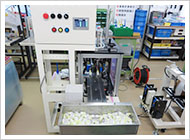

ある化粧品メーカー様からの事例です。
古い機械の再製作
化粧品メーカーが生産ラインで使用している設備の2台目を導入しようとしたところ、製作した会社が廃業しており、お困りになっていました。
そのような中、当社に手元の情報から同じ設備を製作できないかとのご相談を頂きました。
当時、CADデータも残されていない状態でしたが、 断片的に残された手書き図面を頼りに装置を製作することに成功しました。
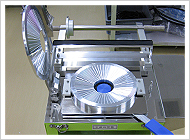

ある化粧品メーカー様からの事例です。
半自動梱包機の作成
様々な化粧品を作っているメーカーですが、その中に石けんの商品があります。全体の売上に占める割合はそれほど多くなく、お金をかけて生産ラインを自動化するのは、現実的ではありません。そのような中、当社に少ない予算で生産効率を上げられないかという相談がありました。
生産ラインの最後に梱包する工程があるのですが、整形された石けんを作業員が手作業で梱包していました。当社では、プレス機に半自動の梱包機を組み合わせて、プレス機で成形された石けんをそのまま梱包できるよう提案いたしました。
既存のプレス機を少し改造し、新たな梱包機を組み合わせられるようにしました。
その結果、少額の投資で梱包工程を大幅に省力化することに成功しました。
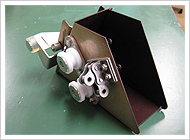

ある食品メーカー様からのご相談事例です。
老朽化した機械の部品供給
生産ラインで使用している古い機械があるのですが、当時の担当者も辞めてしまい、資料も何も残っていない状態でした。
機械は古いものの、まだまだ現役で動いています。とは言え、老朽化しているため、あちこちの部品が摩耗しており、故障することも多くなってきました。部品を交換しようにも、メーカーが既に部品の供給を止めており、入手できない状態でした。そこで、当社の技術者が現場に出向き、実機から図面を起こして、摩耗している部品を作成しました。ただ、同じものを作っただけではなく、元々の部品に改良を加えて、より壊れにくいものにして納品しました。
まだその機械は現役で頑張っているということです。
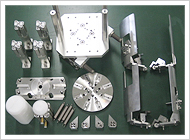

ある事務機器メーカー様の事例です。
メーカーからの供給が終了した部品
生産ラインで使用している機械を作ったメーカーが倒産してしまい、定期的に取り替えていた消耗部品が入手できなくなったとのことでした。
そのため、機械の故障が頻発し、機械稼働率が大きく低下しているとのことでした。導入してまだ減価償却も終わっていない機械でしたので、入れ替えることもできずに、だましだまし使っていたとのことですが、そのような時に当社に相談がありました。
当社で、部品の現物を預かり、同じ部品を供給しました。お客様から余分な部品をストックしたくないというご要望がありましたので、交換時期に合わせて、必要な分だけの部品を供給するようにしています。故障も減り、機械稼働率が上がったと喜んでいただいております。