- Manufacture and modification of labor-saving machines Tsunoda Co., Ltd. >>
- Track record of module production
This section provides several example projects of Tsunoda involving functional module products.
Introduction to functional modules (automation devices)
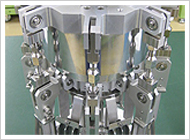
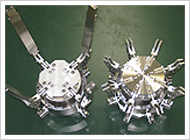

A project for a manufacturer of Western-style confectionery production machines
Western-style confection cutting machine
This customer placed an order with Tsunoda for functional modules, which were robotic arms installed on
their Western-style confectionery cutting machine. Three different types of arms were used to hold the
sweet sugary products before and after they were cut and after they were packaged; the confections came in
various shapes, so the gripping force had to be finely adjusted accordingly.
After discussing and working out all the details with the customer, Tsunoda’s engineers were able to
finally build the three types of robotic arms.
The customer has been greatly pleased with Tsunoda’s solution, because it saved them from having to design
and develop the arms themselves, in addition to simplifying their assembly processes.
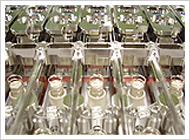
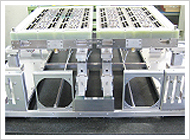

A project for an inspection equipment manufacturer
Functional modules used in inspection equipment for precision parts
This end user was a manufacturer of a wide variety of products in small quantities, making them in various
shapes using the same production line. As their standard stationary jigs could not handle all shape
variations, it placed an order with Tsunoda for stationary jigs as functional modules. Tsunoda’s engineers
were able to create and deliver various types of jigs that would allow the customer to handle all shape
variations. As the types of products the customer has to manufacture constantly change in short cycles,
Tsunoda has been building and delivering new jigs to them ever since.
The customer has been highly satisfied with Tsunoda’s ability to perform detailed customization work
quickly.
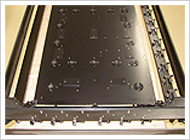

A project for a manufacturer of industrial machinery used to make electronic devices
Glass substrate production line
For this project, Tsunoda started working with the customer from the design phase and developed modular
jigs that were necessary to steadily transport glass substrates on production lines.
The customer needed the jigs to adjust to different glass substrate sizes that varied from one transport
job to the next, and Tsunoda’s technical team achieved this challenging design.
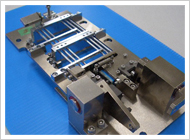
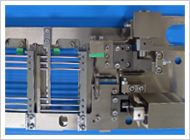

A project for an industrial machinery manufacturer
Battery assembly line
While there were several different machines that are included in this customer’s battery assembly lines,
Tsunoda was requested to manufacture functional modules that would set the battery products in order.
While this customer used to place orders with Tsunoda for individual parts before this project, they were
interested in Tsunoda’s functional module offerings, and started ordering various modular products from
Tsunoda; this involved parts production, assembly, and verification of their precision.
The customer has been highly satisfied, as Tsunoda has helped them reduce costs.