- Manufacture and modification of labor-saving machines Tsunoda Co., Ltd. >>
- Examples of labor-saving projects
This section introduces several example projects of Tsunoda involving labor-saving machines and processes.
The following are just a few of the many projects that Tsunoda has handled in the past.
Tsunoda is confident that it can solve your specific issues.
Even if you have not yet finalized drawings and specifications, our engineers can offer a consultation.
Please feel free to contact us with your inquiry.
Labor-saving in production lines
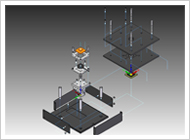

A project for an electronic parts manufacturer
Labor-saving in inspection process
This customer was experiencing much lost time in its inspection process and wanted to solve the problem. As Tsunoda gathered more information, the time loss was found to be due mainly to the inspection set-up: the customer, which manufactured products of various sizes, had to spend much time securing a product for each inspection. Tsunoda developed a fastening jig that could secure inspection objects of varying sizes, thus streamlining the inspection process.

A project for an electronic parts manufacturer
Modification of a washing apparatus
This customer, whose production cycle included a product-drying process, wanted to shorten the drying time
while avoiding uneven drying results. Because the customer manufactured parts that had hundreds of
terminals on each unit, the hot air that was blown onto them could not easily get into all nooks and
crannies, so the drying time had to be prolonged.
Although the customer ran some experiments and found that blowing hot air from a certain angle could
shorten the drying time, it could not transport the products from the production line to the drying
process at the proper angle without raising the cost.
When Tsunoda’s technical team investigated the case, it found the issue could be resolved by modifying the
machine used in the drying process and by creating and installing fastening and vibratory jigs.
After the machine modification and jig construction were completed, the customer was able to reduce the
drying time, while minimizing the rate of defects resulting from unevenly dried parts, with minimal
capital expenditure.
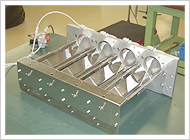

A project for a food manufacturer
Machine used for sealing food container lids
This customer was planning to commercially release a new product, with a unit content smaller than
previous ones. However, as the machine they were using to put the food into individual containers and seal
the lids was optimized for the existing content size, the machine could not be used to handle the new
product as is. The customer considered purchasing a new machine, but decided it would not be
cost-effective. As the new product release date was fast-approaching, they called Tsunoda to help solve
the problem. After reviewing the situation, our technical team determined that the new product could be
handled by modifying the customer’s existing machine.
Tsunoda’s engineers also discovered that the customer’s productivity could be improved by revamping the
operational flow from the food filling process to the container lid sealing process and implementing new
jigs optimized for these tasks, and suggested this.
The customer was able to meet the initial delivery schedule while optimizing its operational efficiency.
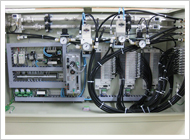

A project involving automobile assembly lines
Modification of a pneumatic circuit control system
This customer was using an automatic painting system, but the color had to be switched for different
models of automobiles. The paint application was pneumatically controlled with this system. High-quality
painting could only be achieved by correctly combining several paint materials and perfectly controlling
the timing of all paint-spraying sequences.
When the customer tested their existing system and found that it could not be continuously used to
properly perform paint jobs on those new automobile models, they contacted Tsunoda’s technical team to
handle the modification work. Even though the modification specifications had to be changed several times
until the project was finished, Tsunoda’s staff maintained close communication with the customer to work
out all the details, which allowed the customer to get the system up and running when the new vehicle
production started.
This successful project by Tsunoda helped the customer handle the new product rollout according to plan,
at little extra cost.
Automation of manual production tasks
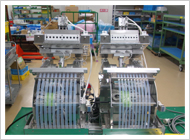

A project for an electrical equipment manufacturer
Modification of a parts conveyor system
This customer’s production line included a process where parts to be assembled were manually placed onto a
belt conveyor one by one. This not only caused high labor costs but also entailed the risk of
manually-placed parts falling over during transport, forcing the line to stop each time. To solve this
problem, the customer asked Tsunoda to automate this manual task.
Tsunoda’s technical team suggested an apparatus that could stock parts in its top section and feed them to
the production line in a synchronized manner one by one, so that they would never fall over while in
transit.
By implementing this solution, the customer was able to reduce labor on the production line from four
persons to two, and effectively eliminate parts supply errors that interrupted the production line.
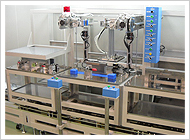

A project for a metal parts manufacturer
Machine for transporting and turning over heavy objects
This customer’s assembly line included a process in which parts, each weighing over 60 kg, had to be
brought on, which was handled by three workers. In addition, once the top section of each unit was
assembled, the three workers had to lift it up and reverse it so that the bottom section could be
assembled. This arrangement was inefficient as the task of assembly could be handled by one worker, but
each time the aforementioned lift-and-reverse maneuver became necessary, other workers had to stop what
they were doing and help the assembly worker. Furthermore, the customer was concerned about the risk of
accidents as workers handled heavy parts this way, although no major accident had occurred before.
To address these issues, Tsunoda developed and delivered an apparatus that could not only place the heavy
parts onto the production line safely but also automatically turn them over midway through the assembly
process.
By introducing this apparatus, the customer’s workers no longer had to interrupt their individual tasks,
which improved both their work efficiency and safety.
In addition, the apparatus allowed them to manufacture even larger products, thereby expanding their
product range.
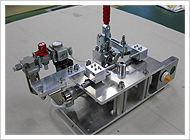

A project for a light bulb manufacturer
Efficiency improvement by new jig implementation
While each light bulb has parts called a metal cap (base) and an eyelet, production workers at this
customer separately assembled them by hand. To streamline the process, Tsunoda’s engineers developed a
mechanical jig that could simultaneously crimp these metal caps and eyelets. Although it was technically
possible to automate all of the customer’s assembly lines, there was not enough budget. Therefore, Tsunoda
focused on building the jig without modifying the existing equipment, and was able to integrate the two
separately handled assembly tasks into one.
By semi-automating this most time-consuming process, the customer was able to improve the efficiency of
its production lines at minimal cost, and is satisfied with the results.
Machine and equipment modification
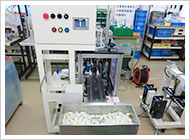

A project for a cosmetic manufacturer
Replication of old machinery
This cosmetic-producing customer was using an apparatus on its production line and wanted to order a
second unit from the manufacturer but found they had gone out of business.
The customer found out about Tsunoda and asked us if we could make the same apparatus from the available
information that remained.
Even though there was no CAD data for the apparatus, Tsunoda’s engineers managed to successfully build a
second unit of the same apparatus based on handwritten drawings that only covered portions of the
apparatus.
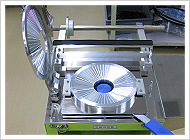

A project for a cosmetic manufacturer
Construction of a semi-automated packing machine
This customer manufactured a whole range of cosmetic products, including soaps which only accounted for a
small percentage of their total revenue, so could not spend much on automating their soap production line.
As the customer still wanted to improve its soap production efficiency with a limited budget, they came to
Tsunoda for a consultation.
Tsunoda’s technical team noticed that there was a packing process at the end of the production line, which
involved workers manually placing finished soap products into boxes. To streamline this process, Tsunoda
devised and proposed a solution that would combine their press machine with a semi-automated packing
machine so that the molded soaps coming out of the press machine could be packaged immediately.
This solution only required a slight modification of the customer’s existing press machine, so it could be
docked with a new packing machine.
This allowed the customer to significantly improve the efficiency of the packing process with only a small
investment.
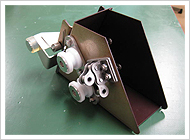

A project for a food manufacturer
Supply of parts for legacy machinery
This customer was still using an old machine on its production line, but the staff who had procured it had
already left the firm, and there were no documents about the machine.
Although the machine was old, it still worked and was good enough for the task, but a number of parts had
worn out over the years and it had started malfunctioning more often. The customer wanted to replace those
worn parts but the manufacturer had discontinued them. So, Tsunoda’s technical crew visited the shop
floor, created schematic drawings by directly observing the machine, and crafted the parts. Those parts
were improved versions of the original ones and were more durable.
According to the customer, the machine still works fine since the parts were replaced.
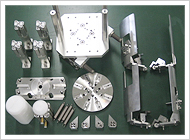

A project for an office equipment manufacturer
Parts no longer available from the original manufacturer
One of the machines on the customer’s production line malfunctioned, but the manufacturer had gone
bankrupt, and consumables that needed to be replaced periodically were no longer available.
As the machine malfunctioned more often, the machine work rate fell. The customer considered replacing the
faulty machine, but had bought it only recently, and the value had not fully depreciated. So the customer
contacted Tsunoda for a consultation, as the machine was not functioning properly.
Tsunoda’s team of engineers borrowed its parts, succeeded in replicating them, and supplied them to the
customer. As the customer was reluctant to keep too many of them in inventory, Tsunoda agreed to supply
the spare parts periodically in only the required quantities. The customer was highly satisfied with the
outcome, as the machine’s failure rate has dropped and its work rate has improved sharply.